19 Aug Blast Off – Restoration with Micro-abrasive blasting
Micromanufacturing Fall 2009, Volume 2, Issue 3
Similar to applying abrasive grits bound together on a grinding wheel, many part manufacturers view micro-abrasive blasting as an art form shrouded in mystery. That’s because of the high level of operator control required to effectively smooth, deburr, texture, peen or clean microparts—among a host of applications— without damaging or destroying them.
Process parameter
According to Jawn Swan, president of Crystal Mark, Inc. six factors primarily control surface finish when abrasive blasting: the type of abrasive particle, abrasive size, air pressure for delivering the abrasive, amount of abrasive going into the air-stream, nozzle size and the nozzle tip’s distance from the work-piece.
Various abrasive powders are available in a range of sizes. Crystal Mark, Inc. a Glendale, Calif., manufacturer of blasting equipment and job shop, offers silicon carbide, aluminum oxide, white Al2O3, crushed glass, glass beads, Dolomite, plastic blast and sodium bicarbonate. Although the process is sometimes called “micro sandblasting,” applying sand as a media is not an option. According to Swan, the company offers the abrasives in standard sizes from 12μm to 80 grit and can tailor abrasive sizes to suit a customer’s application. Although Crystal Mark’s smallest standard size is 12μm, Swan said the company’s equipment can feed particles as small as 1μm, adding that limited applications exist for that abrasive size and a HEPA filter is needed to collect the particles. “The federal government has said particles 10μm and smaller are a health hazard,” he said.
Another blasting application with glass beads involved a 16″×12″ convex tertiary mirror for a satellite. Swan explained that the mirror assembly includes an antenna that gathers microwave signals from Earth and the mirror directs them to an instrument package, but when the antenna points directly at the sun, the powerful solar frequencies can damage the instrumentation. Crystal Mark, Inc. was able to blast the mirror to impart a surface finish that allows transmission of the needed microwave frequencies but not the solar ones. Swan added that the surface had a mirror finish prior to blasting and a matte finish afterwards. To illustrate how different work piece materials require different media when blasting, Swan noted that two implant samples Crystal Mark, Inc. processed for a medical device company, which measured about ⅝” in diameter by ⅜” high and had a ¼”-dia. hole in the middle, were identical except that one was made of titanium and the other PEEK (Poly- EtherEtherKetone) plastic. “Broaching the titanium implant kicked up some pretty good-size burrs,” he said. “We removed those burrs using glass beads. Th e PEEK part had feathery burrs all over it; we used sodium bicarbonate as the abrasive material.”
Swan added that because glass is harder than sodium bicarbonate, with a 5.5 Mohs hardness for glass vs. a 2.5 Mohs hardness for the latter, glass is able to peen titanium while deburring the metal, whereas applying sodium bicarbonate would take an excessive amount of time to achieve those results—if it were even possible. On the other hand, sodium bicarbonate’s sharp crystal structure can slice the feathery burrs from PEEK without impinging into the work-piece material, which can occur with other abrasives, such as Al2O3. In addition, sodium bicar-bonate is water soluble, so any abrasive remaining on the implant can be removed via washing. The typical pressure that most microblasters use is fixed at 140 psi, according to Swan, but it can be as low as 1 psi and as high as 250 psi. “Not a lot of work gets done at 1 psi,” he said.
Blasting High and Higher Art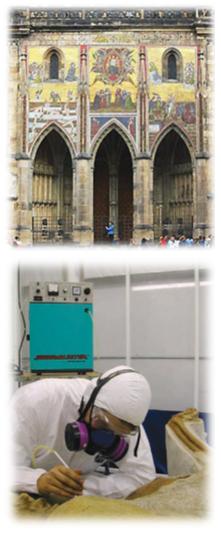
MANY MICRO-ABRASIVE blasting applications don’t involve precision machined or plastic injection-molded parts. Many involve cleaning fossils, restoring artwork and creating arts and crafts—to name a few. A video about the later is available at Crystal Mark Inc.’s Web site. It shows intricate designs being blasted into an eggshell using a 0.018″-dia. nozzle to deliver 50μm aluminum-oxide abrasive at 100 psi. The company’s Jawn Swan added that Crystal Mark, Inc. supplied materials used in restoring “The Last Judgment” mosaic on the south façade of St. Vitus Cathedral in Prague Castle. The triptych mosaic measures 904 sq. ft. and was completed in 1371. “We sold them tons and tons of crushed glass to do that, along with four pieces of equipment,” Swan said. According to the Getty Conservation Institute, which collaborated with the Office of the President of the Czech Republic on the 1998-to-2000 project, the mosaic’s brilliant colors were rendered invisible by a layer of corrosion that repeatedly formed after each past cleaning and restoration. “By choosing the proper abrasive material, they were able to remove the failed restoration attempts and remove the oxidized glass but not damage the good glass,” Swan said.
A fossil preparer removes debris from a fossil using micro-abrasive blasting.
Know your nozzle
As previously noted, nozzle size is a primary factor in controlling surface finish. Available sizes vary according to the manufacturer. For example, Crystal Mark, Inc. makes standard round carbide nozzles with IDs from 0.007″ to 0.060″ and rectangular carbide ones from 0.006″×0.020″ to 0.008″×0.150″. Most standard nozzles are straight. But, to permit access to difficult-to-reach part areas, 45°- and 90°-angle styles are also offered. Nozzles with extended tips are another option. Changing the amount of abrasive that’s entering the air-stream will make the blasting process faster or slower, but too much abrasive can inadvertently slow the process, Swan noted. “If you have more particles in there than gas, you reach a point where you’re not getting enough speed out of the particles,” he said. Changing the amount of abrasive that’s entering the air-stream will make the blasting process faster or slower, but too much abrasive can inadvertently slow the process, Swan noted. “If you have more particles in there than gas, you reach a point where you’re not getting enough speed out of the particles,” he said.
Manual vs. automatic
Operators often perform abrasive blasting with a hand held pencil blaster. For some simpler applications, an inexperienced operator can develop good technique in as little as 10 minutes. Automated blasting equipment is also available. The Belt Abrader from Crystal Mark is a conveyorized system with one to six nozzles reciprocating across the conveyor belt, which moves linearly. Such a system is appropriate for delicate parts that require the surface finish to be consistent across the entire substrate, and it can produce features such as round and rectangular holes, Swan said. Swan added that the smallest part Crystal Mark’s job shop blasts on a regular basis is a little stud component with a 2-56 thread for a jet engine. “I don’t know if I found the smallest part yet,” he said. “Micro-abrasive blasting is a tool that there are a lot of applications for. My job is to find those applications.” By gaining knowledge of micro-abrasive blasting, the mystery shrouding the process can be removed and even microparts can be efficiently blasted to the needed specification.
What to read the entire article? Click here
About the author:
Alan Richter is senior editor of MICROmanufacturing. Telephone: (847) 714- 0175. E-mail: alanr@jwr.com.