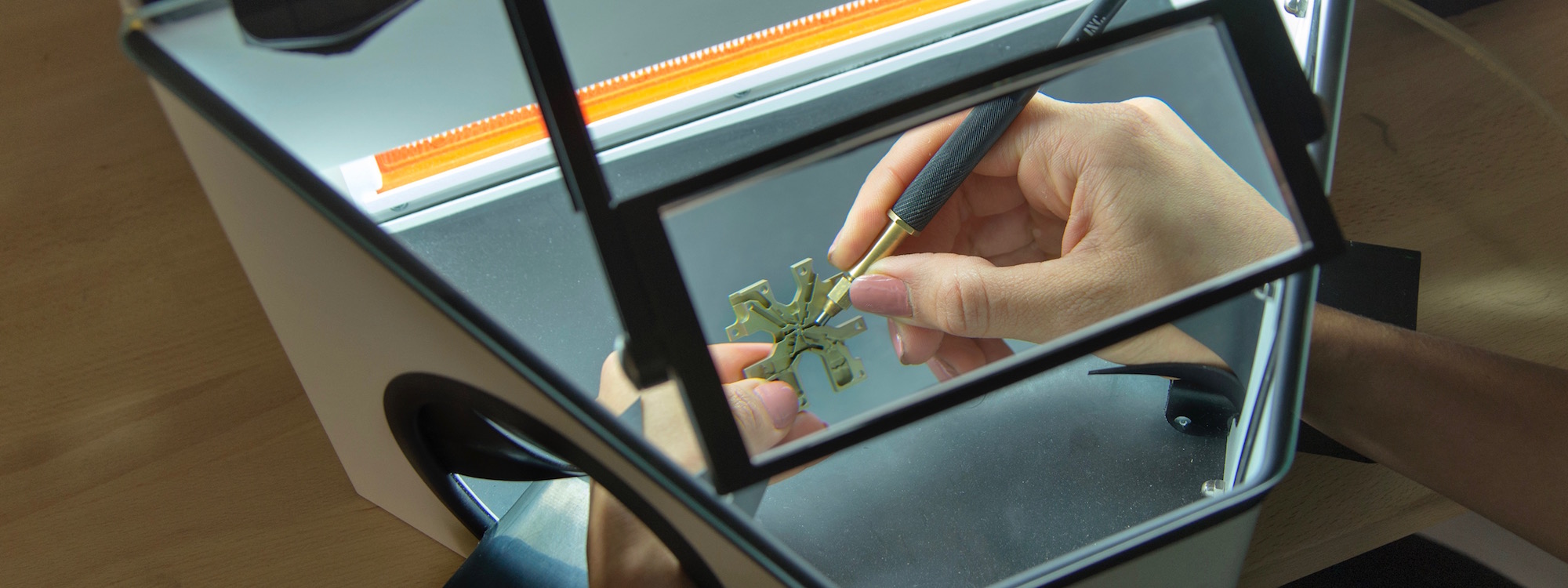
07 Aug Control Variable #2 of 5: Blast Pressure
In the micro abrasive blasting process, precision graded abrasive particles are introduced into a stream of compressed gas. The mixture is transported through a hose and focused through a small nozzle, aimed at the area to be abraded.
After the type of abrasive used, Blast Pressure is the next major variable in the process. Although Blast Pressure determines the velocity at which the abrasive particles travel, it has different ramifications depending on the application.
During selective removal like preparing a fossil or stripping coating from a PCB where it is critical to preserve an underlying structure, the pressure setting needs to be in the “Goldilocks ZONE”: not too high, not too low.
The same applies to surface finishing: too high a pressure can result in particle impingement instead of intended surface alteration. If the pressure is too low, the target surface finish is not achieved.
- The higher the carrier gas pressure is, the greater the velocity of the abrasive particles which results in more aggressive abrading.
- When a less aggressive result is desired, the carrier gas pressure is reduced, reducing the velocity of the abrasive particles thus causing less material removal upon impact.
- The type of the carrier gas used can alter the particle velocity as well. Compressed air with aluminum oxide cuts glass approximately 30% faster than carbon dioxide.
- After the abrasive particle size and type, the Blast Pressure is the next most critical variable directly impacting development of static electricity. Effective control of electrostatic discharge (ESD) can be critical for applications such as conformal coating removal, medical electronics, micro machining of silicon devices, MEMS, etc.
Crystal Mark’s SWAM® micro abrasive blasters provide true control with independent Blast Pressure regulation and Powder Flow Control. More on powder flow control in variable #4 Powder to Carrier Gas Ratio.
Blast Pressure range:
- Standard range available on Crystal Mark products: 5 -125 psi
- For customer specific applications, the team has developed equipment modified to use blast pressures below 1 psi, or as high as 300 psi.
Precise consistent control over the Blast Pressure at which the abrasive is applied to the area being processed is critical for success with most micro abrasive applications. The Crystal Mark team works closely with customers to analyze the application and recommend precise process parameters.
The next blog post in this series talks to the third control variable: Nozzles.
CONTROLLING A MICRO ABRASIVE PROCESS – FIVE VARIABLES:
FOUR: Abrasive to Carrier Ratio
FIVE: Speeds and Feeds