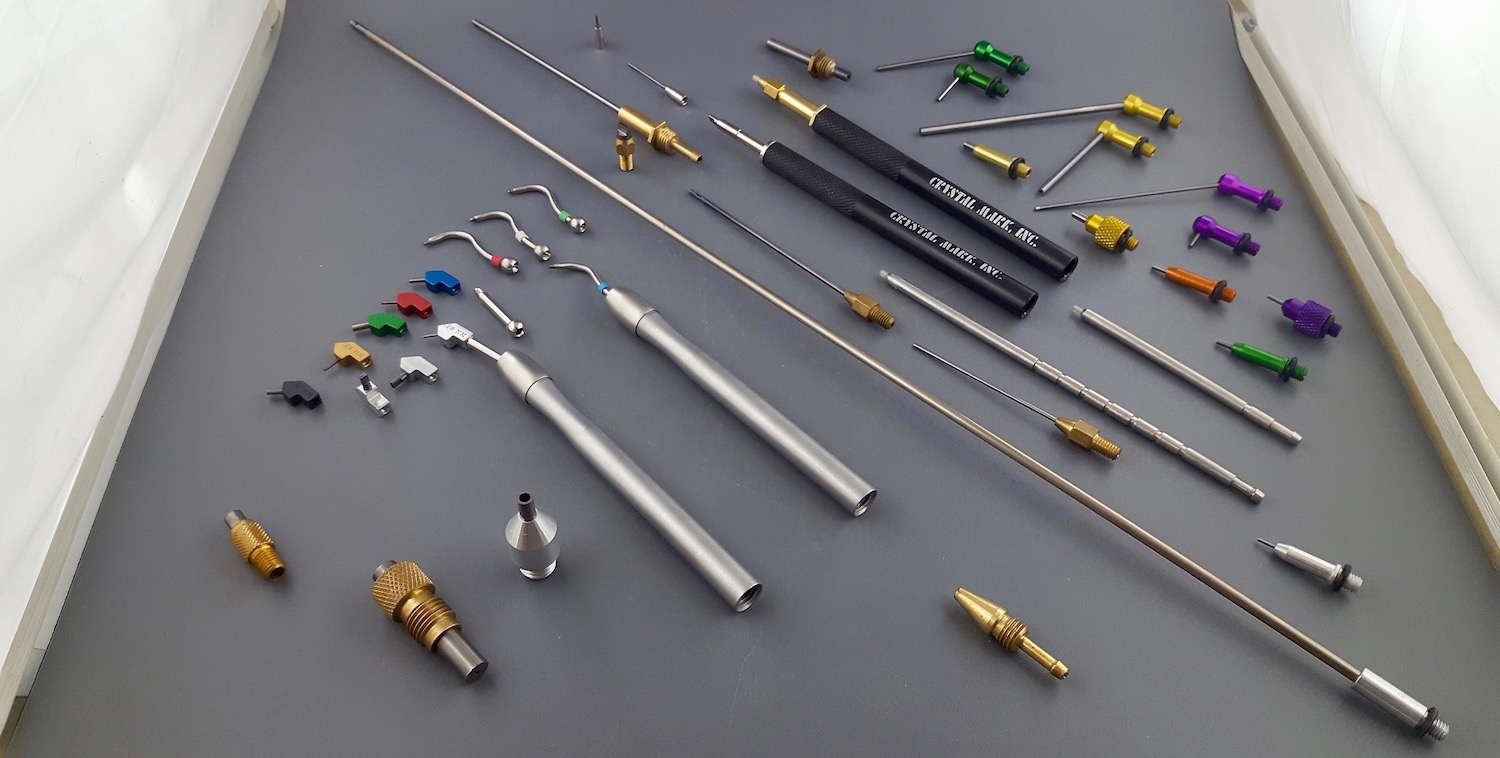
19 Oct Control Variable #3 OF 5: Nozzles
The micro abrasive process can provide unparalleled precision and consistent repeatability by aiming a focused stream of compressed gas and abrasive through a nozzle.
This blog post talks about #3 of the 5 variables that govern the micro abrasive blasting process – Nozzles. In micro abrasive blasting, nozzles play a key role in achieving the objectives for any process.
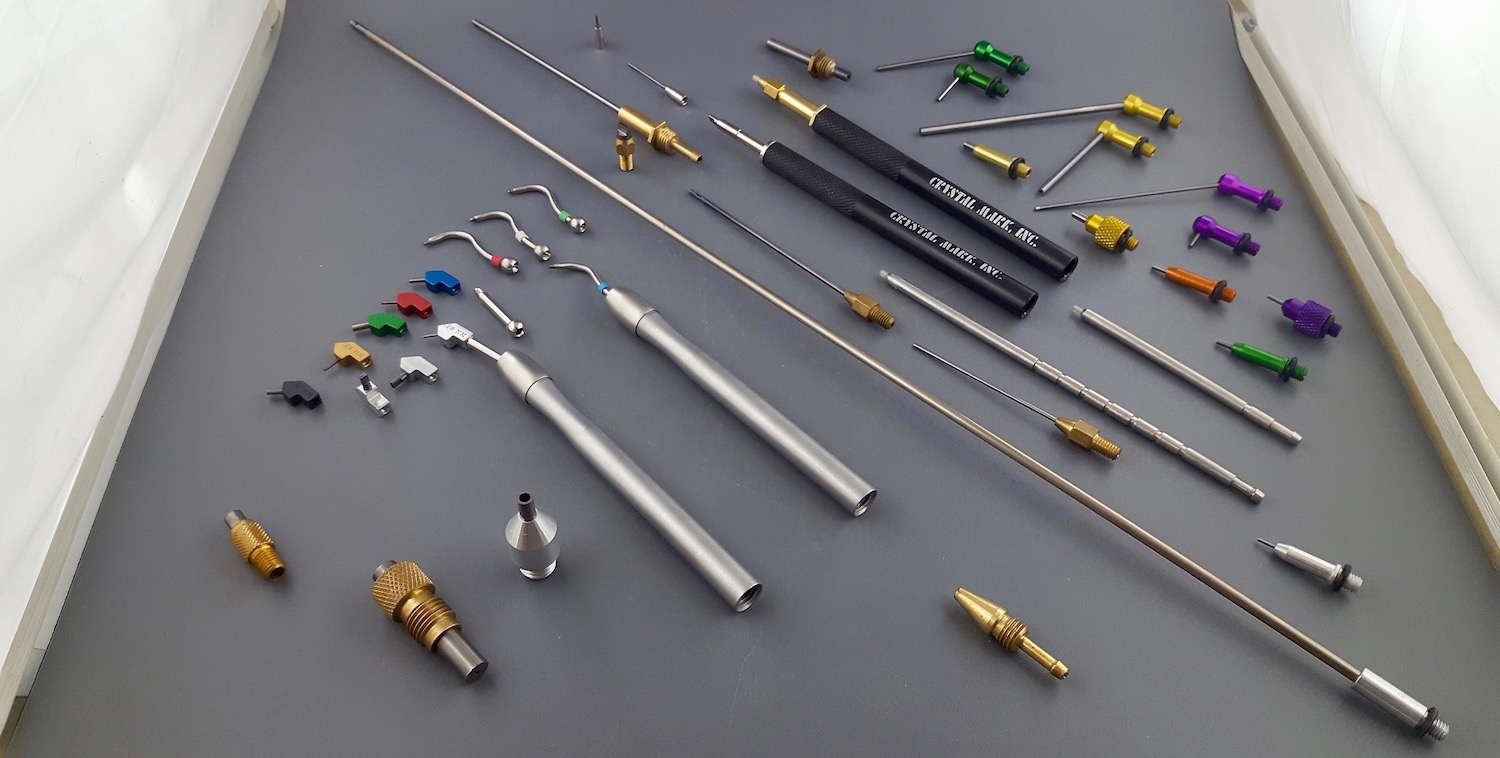
Crystal Mark Nozzles: Critical Control Variable for Required Accuracy, Precision & Control for Any Micro Abrasive Process | Extensive Range of Pre-designed Nozzles | Ability to Customize Nozzles Size, Shape, Material Properties as Required
WHAT DO YOU LOOK FOR WHILE SELECTING THE RIGHT NOZZLE FOR YOUR SPECIFIC APPLICATION?
ONE: Size of the Target Area to be Processed
Crystal Mark can provide nozzles as small as 0.005” round or 0.0065” square, to as large as 0.125” round or 0.150 x 0.020” rectangular for all applications.
TWO: Shape of nozzle
- For most of the applications (95%), round nozzles work best.
- In specific applications that require a linear cut, the team has been able to develop rectangular nozzles. For example, thick film resistors are trimmed in this way.
- When precise control is required on surfaces deep within complex parts, Crystal Mark can develop custom side cutting nozzles designed to target the intended area.
- Crystal Mark has designed long nozzles for removing casting investment or deburring inside very small diameter hollow spaces like the veins in jet engines or turbines.
THREE: Material to be used for manufacturing the nozzle
- Crystal Mark is able to manufacture nozzles using tungsten carbide, sapphire, or other exotic composite materials as required for specific applications.
- Sapphire nozzles can last 4 to 7 times longer in certain conditions such as use of very fine Aluminum Oxide (35 microns or finer).
- For most applications, tungsten carbide is the material of choice.
FOUR: Nozzle tip distance to the part
The mixture of the compressed gas and abrasive expands outward as soon as it leaves the nozzle. The diameter and shape of the nozzle plays a key role in achieving the right results for the intended process.
- The greater the distance the nozzle is from the intended substrate the wider the abrasive pattern.
- Peak particle velocity happens between 1/8 to 1/2” from the nozzle tip. Good for cutting.
- When using masks and controlling an etch depth into a substrate, it is beneficial to have the nozzle 1-1/2 to 3” from the part.
- For surface abrading for aesthetics, improved adhesion or cleaning the target distance should be 2 to 6” from the part.
The above are suggested guidelines or a starting point for developing new processes. Certain applications may deviate from the standards above.
THE CRYSTAL MARK ADVANTAGE:
Over the past 50 years, Crystal Mark has developed an extensive inventory of standard nozzles to support a wide range of applications. The team uses refined methodology to select the right nozzle and abrasive for every application. Their in-house design team and machine shop can custom manufacture nozzles quickly and at an affordable cost. This provides unparalleled flexibility and control.
The next blog post will talk about # 4 of the 5 Variables in Micro Blasting: Abrasive to Carrier Ratio.
CONTROLLING A MICRO ABRASIVE PROCESS – FIVE VARIABLES:
FOUR: Abrasive to Carrier Ratio
FIVE: Speeds and Feeds