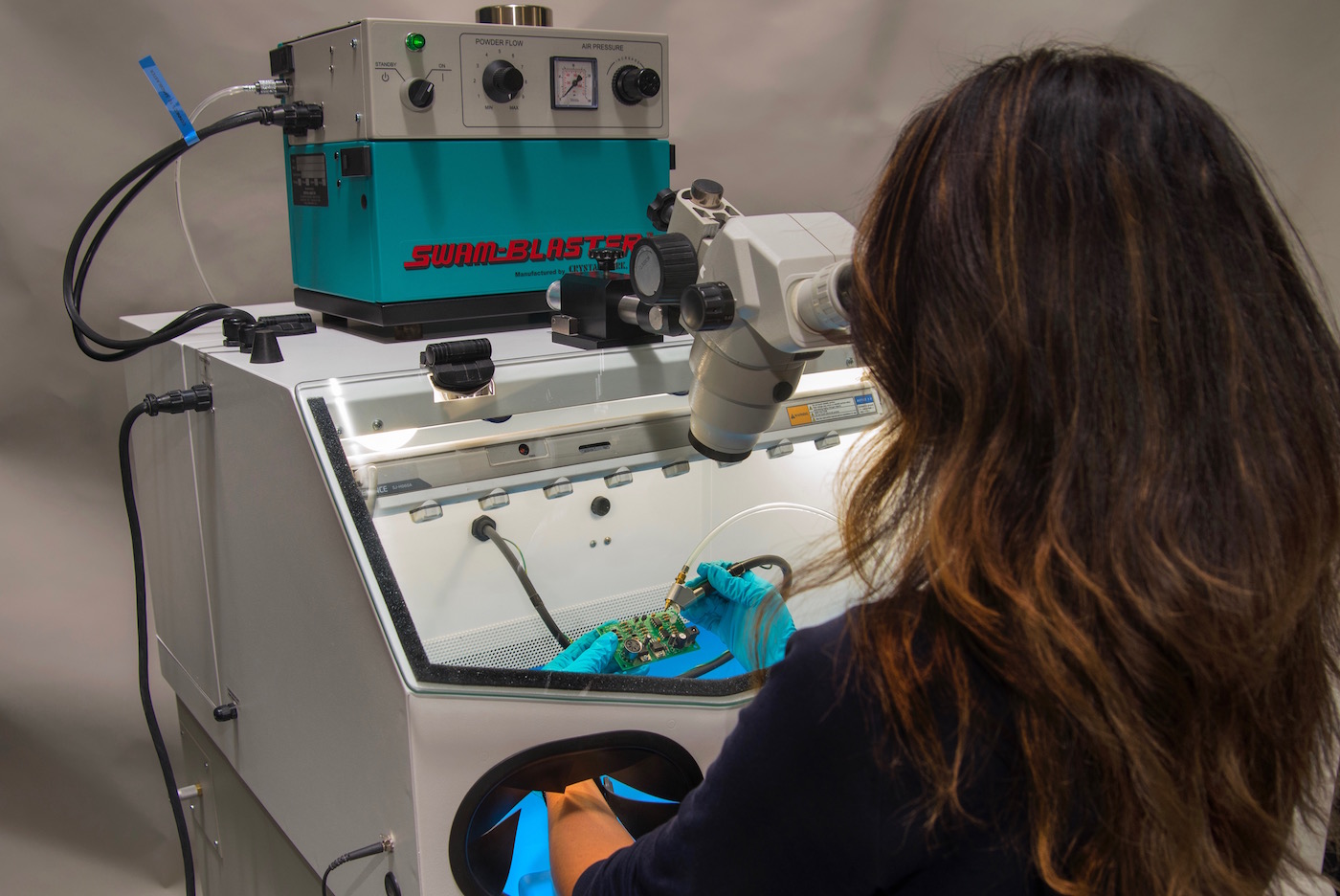
07 Mar Control Variable #4 of 5: Abrasive to Carrier Ratio
In micro abrasive blasting, a focused stream of compressed gas and abrasive is aimed at the target area to be processed. The compressed carrier gas imparts the necessary kinetic energy upon the abrasive particles to effectively carry out the micro abrasive process.
The ratio of the abrasive to the carrier gas in the stream plays a critical role to achieve the desired results.
For applications such as surface finishing, cleaning, texturing, deburring, or conformal coating removal (CCR), a higher proportion of abrasive in the stream achieves the desired process objective more efficiently.
For drilling, cutting or working down inside small structures, the micro abrasive process requires more air and less powder. For small features with limited access to the target process area, less amount of abrasive can make it easier to extract out the used abrasive particles and the target substrate.
Crystal Mark, Inc. SWAM® technology uses a unique vibratory feed system that allows the equipment to feed a wide variety of abrasives at any pressure an application requires. This is an advantage for Crystal Mark customers over other micro abrasive blasting technologies that rely on differential pressure to deliver the abrasive powder.
The SWAM® Blast abrasive powder induction system provides truly independent, precise control over the volume of abrasive powder introduced into the carrier gas at any pressure.
This allows for the widest possible window of parameters available in the industry:
- It can feed much finer sizes of abrasive particles even down to the sub-micron level for high precision applications.
- It also allows for the use of much smaller size nozzles down to 0.005 inches or 125 microns.
- And at pressures as low as ½ a psi or 3.5 kilopascal.
Maintaining the right ratio of abrasive to carrier gas is critical to the success of any micro abrasive process. The Crystal Mark, Inc. team works closely with customers to understand their process objectives, and come up with the most optimal ratio of the abrasive to carrier gas.
In the next blog post in this series, we will talk about #5 of the 5 control variables in micro abrasive blasting – Speeds and Feeds.
CONTROLLING A MICRO ABRASIVE PROCESS – FIVE VARIABLES:
FOUR: Abrasive to Carrier Ratio
FIVE: Speeds and Feeds