
19 Jun Control Variable #1 of 5: Abrasive Powder
In micro abrasive blasting, precision graded abrasive particles combined with a stream of compressed gas are focused through a nozzle aimed at the surface to be processed.
This blog posts talk about #1 of the 5 variables that Govern the micro abrasive blasting process – Control the Abrasive. For effective, consistent and precision results, it is critical that you select the proper abrasive for the micro sandblasting application. The four major variables in abrasive to consider are:
- Material properties
- Particle size
- Shape of abrasive particles
- Consistency over large volumes, and over time
ONE: Material Properties – Hardness and Weight
With many different types of abrasive material available in the open market, how do you determine which one is right for your application? The correct abrasive should be able to achieve the required surface finishing or stripping without damaging the target substrate. Some materials are heavy and soft like Iron Shot while others are extremely hard and light like Cubic Boron Carbide. Yet others are soft and light like Plastic Abrasive or heavy and hard like Aluminum Oxide. So which is the correct abrasive for you? Crystal Mark has a refined methodology to analyze the requirements for your micro abrasive application, and provide the right abrasive. When required, the Crystal Mark team is able to develop custom blend abrasive materials for the specific application.
TWO: Particle Size
“The bigger the bolder, the greater the crater.” Keith Swan, VP of Operations. A coarse abrasive will work faster, remove more material and create a rougher surface finish than a fine material. However, there is always a tradeoff. Is the large, fast cutting particle damaging your product or affecting your process yield? If it is, Crystal Mark, Inc. manufactures blasting equipment that can feed abrasives with particle sizes ranging from sub-micron levels up to 500 micron. However, in micro-blasting, they are typically using 120 grit and finer. The technicians at Crystal Mark, Inc. can recommend the right size abrasive for your substrate based on predicate knowledge or run a DOE in their Abrasive Lab to identify the optimal media size for your application.
THREE: Shape of the Abrasive Particles
Depending upon the type of substrate and surface finish requirements, it helps to select the right shape of abrasive particles.
Example One: Three different shape profiles of 60 Grit Aluminum Oxide
Left: Spear shaped Aluminum Oxide at high pressure can impinge on certain substrates but works well for removing rubbery or soft coatings off of hard surfaces.
Middle: Angular shaped Aluminum Oxide is good for machining both crystalline and amorphic substrates.
Right: Blocky shaped particles are used primarily for deriving specific surface finishes.

60 Grit Aluminum Oxide shown in 3 different shape profiles
Example Two: 60 Grit Glass Bead Spherical
Glass bead works similar to shot peening. Blasting with spherical media can work to harden surfaces and brighten up other blasted surface finishes primarily to increase strength and for aesthetic purposes.
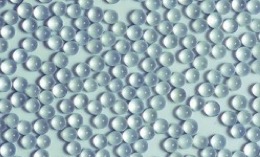
60 Grit Glass Bead | Spherical Shape
FOUR: Consistency over Large Volumes, and over Time
It is very important to make sure your blast media or abrasive has a similar particle distribution from one lot to the next. You want it to work the same today as it does next week and next year. The Crystal Mark in-house Abrasive Lab goes to great lengths to ensure consistency in quality of the abrasives they sell. Crystal Mark will also provide certification for the abrasive upon request.
The team is able to provide Lab Analysis report for the customer’s abrasive sample.
A key to success with micro abrasive blasting process: “If you fail to control the abrasive, you fail in controlling your process.” Jawn Swan, President of Crystal Mark, Inc.
The next blog post will talk about # 2 of the 5 Variables in Micro Blasting: Blast Pressure.
CONTROLLING A MICRO ABRASIVE PROCESS – FIVE VARIABLES:
FOUR: Abrasive to Carrier Ratio
FIVE: Speeds and Feeds